Contact surface requirements
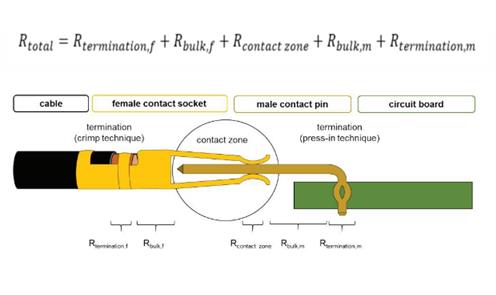
Plug in connectors are used in a variety of different environments, such as hot or humid. They are also used in adverse environmental conditions such as corrosive environments. Therefore, the contact surface of electrical contact must meet various requirements. The purpose is to improve the performance of the contact substrate, especially the corrosion resistance of the substrate. Due to the corrosion of the substrate, heterogeneous layer will be formed, which leads to the change of electrical characteristics, that is, the increase of film resistance. In order to limit the influence of these heterolayers, the substrate should be coated. Compared with the uncoated substrate, the force required to break the heterogeneous coating can be reduced.
The coating must also have high conductivity, thermal conductivity, and low friction and wear. However, high wear resistance is always a compromise between low insertion force and pull-out force.
There are two main wear mechanisms. On the one hand, the mechanical wear of the contact surface is caused by the insertion operation, which will lead to the exposure of the non precious metal interlayer or even the base material of the contact surface after a period of time, thus making it more prone to corrosion. On the other hand, fretting wear of the contact surface caused by temperature change or vibration will lead to small oscillation motion (fretting < 125 μ m). Therefore, it is necessary to construct high resistance corrosive products, such as oxides, in the contact interface to produce fretting corrosion. In the case of precious metal contact, fretting corrosion will begin when the contact surface is worn and the nickel interlayer or copper alloy has been exposed. Non noble metal contact surfaces, such as tin, are generally prone to fretting corrosion